The 5 METALLICO Processes
In METALLICO, 5 innovative processes will be developed. They will be used to recover and exploit the (critical) metals relevant for METALLICO from primary and secondary resources. The processes will be evaluated in terms of their sustainability.
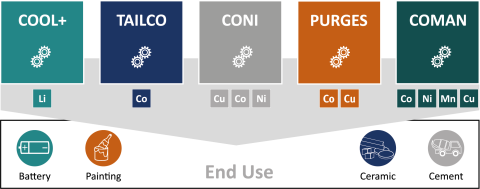
The 5 processes and their end use.
Learn more about the 5 METALLICO Processes in our graphics