COOL+ Process: Lithium carbonate production in battery grade
2 December, 2024
TU Bergakademie Freiberg (TUBAF), in collaboration with Fraunhofer IKTS, has successfully validated a process for recovering lithium from primary sources, demonstrating efficacy not only in laboratory but also at a pilot scale. The selective recovery of lithium from spodumene ore is achieved through the innovative COOL+ process.
The COOL+ process involves a leaching step that utilizes supercritical CO2, enabling the extraction of lithium in a more efficient and environmentally friendly manner. The spodumene ore used in the process contained a lithium concentration of 2.86 wt.%. To enhance the mobilization of lithium during the digestion phase, sodium carbonate (Na2CO3) was added, which played a crucial role in activating the ore thermally. Following the digestion step, the resulting mixture was subjected to filtration, separating the lithium-rich solution from the solid residues.
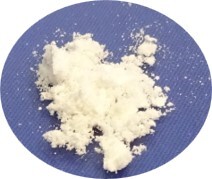
Lithium carbonat obtained in the COOL+ process. @TUBAF
Once the lithium-rich solution was obtained, it underwent a concentration step to further purify the lithium content. This was followed by a washing process that culminated in the production of lithium carbonate (Li2CO3), which meets battery-grade specifications with a purity level of 99.7% or higher. This high-quality lithium carbonate is well-suited for applications in the battery industry, particularly in the production of lithium-ion batteries. In addition to lithium recovery, the COOL+ process also addresses sustainability concerns since the solid silicate residue that remains after the CO2 leaching step is not wasted; instead, it is repurposed to produce geopolymers. This approach aligns with the principles of circular economy and zero-waste, as it not only facilitates the recovery of valuable and critical raw material like lithium but also generates an additional product suitable for the construction industry. By developing and validating the COOL+ process, TU Bergakademie Freiberg and Fraunhofer IKTS are contributing to a more sustainable resource management within the lithium supply chain in Europe.
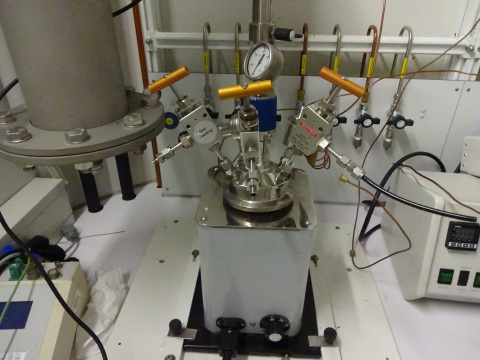
Autoclave for lab-scale (1 L) at TUBAF; @TU Bergakademie Freiberg
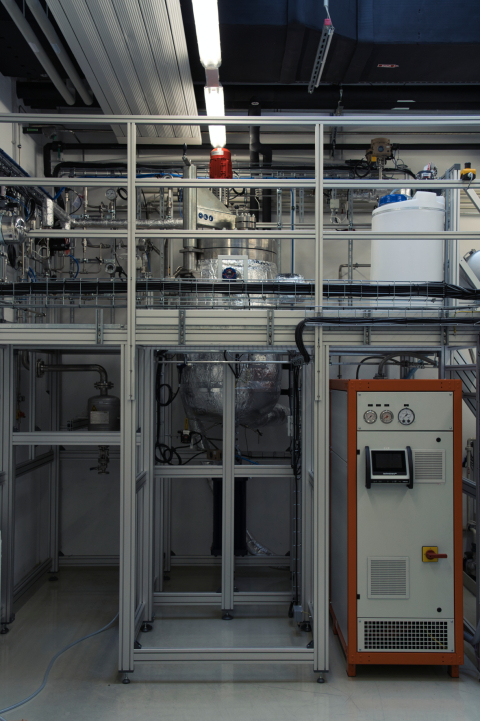
Autoclave reactor (200 L) at IKTS. @Fraunhofer IKTS
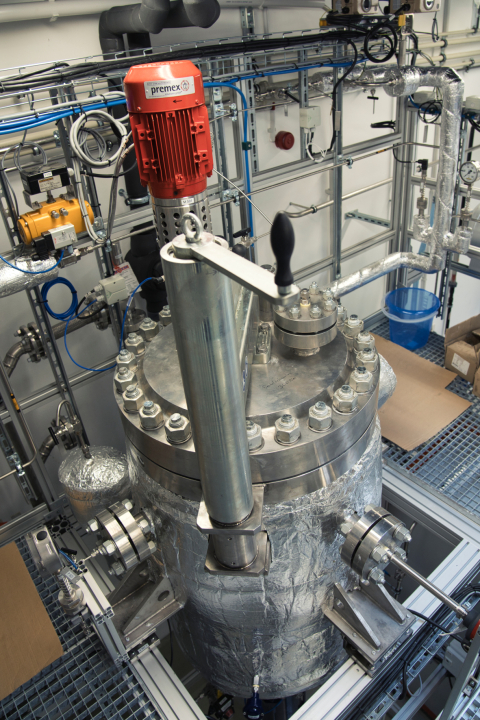
Autoclave reactor (200 L) at IKTS. @Fraunhofer IKTS